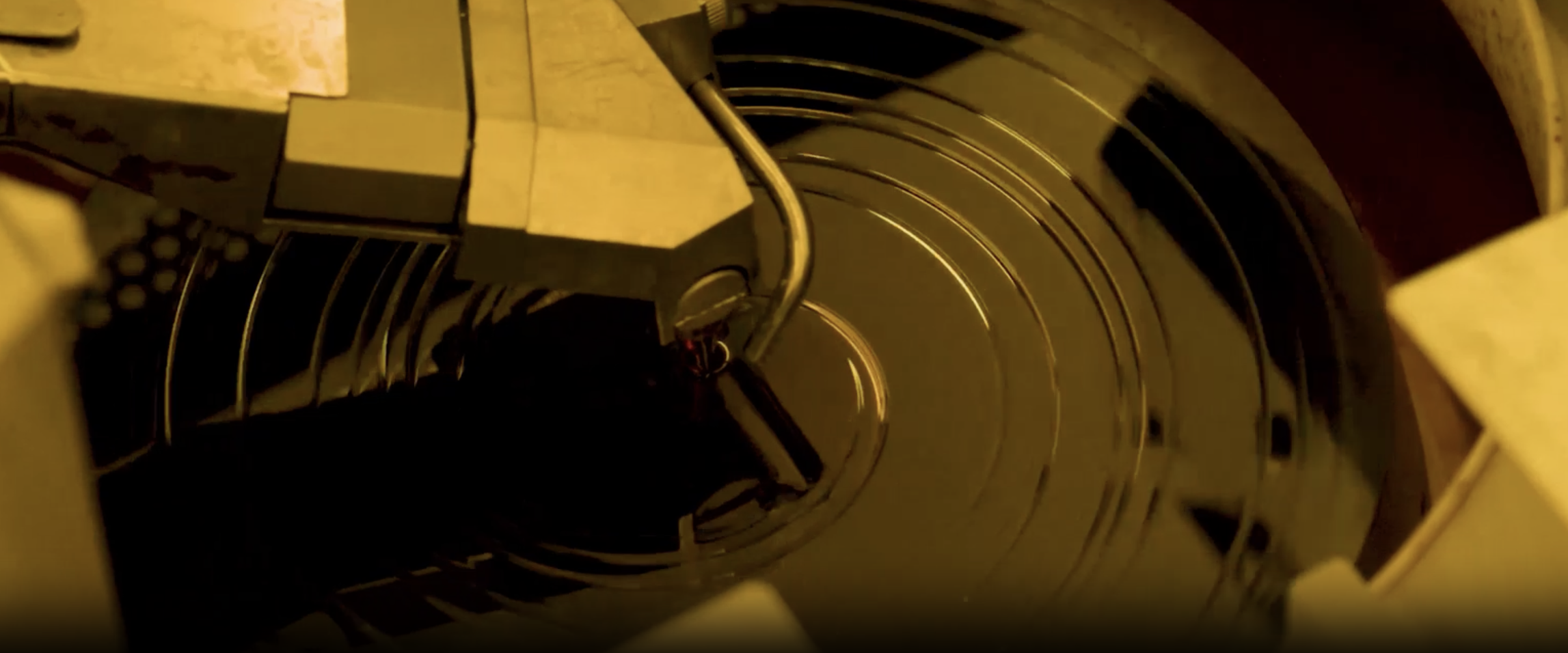
Advancing solutions to
critical research challenges
ASU Core Research Facilities provide access to advanced equipment, in-depth consultation and individualized services to help you achieve your research goals on any budget, scale or timeline.
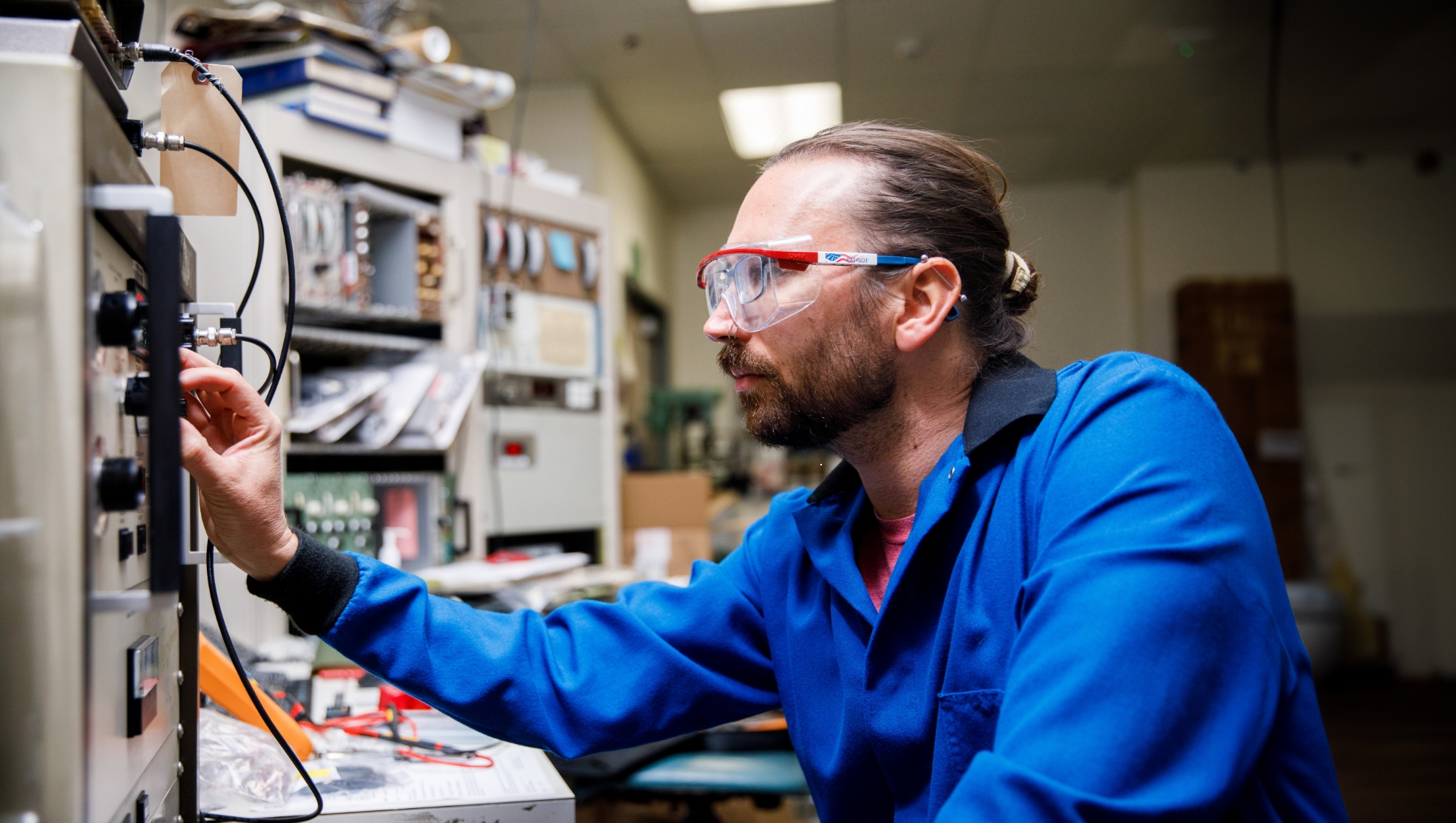
We are a cost effective, one stop shop that translates ASU's transdisciplinary expertise and wide array of equipment into solutions for each client.
- 30 distinct facilities in six focus areas.
- State-of-the-art equipment and in-depth expertise.
- Go-to destination for academic researchers and businesses.
Whether you're a two-person startup or a Fortune 500 company, our streamlined, pay-for-use model and flexibility can holistically cover your research needs.
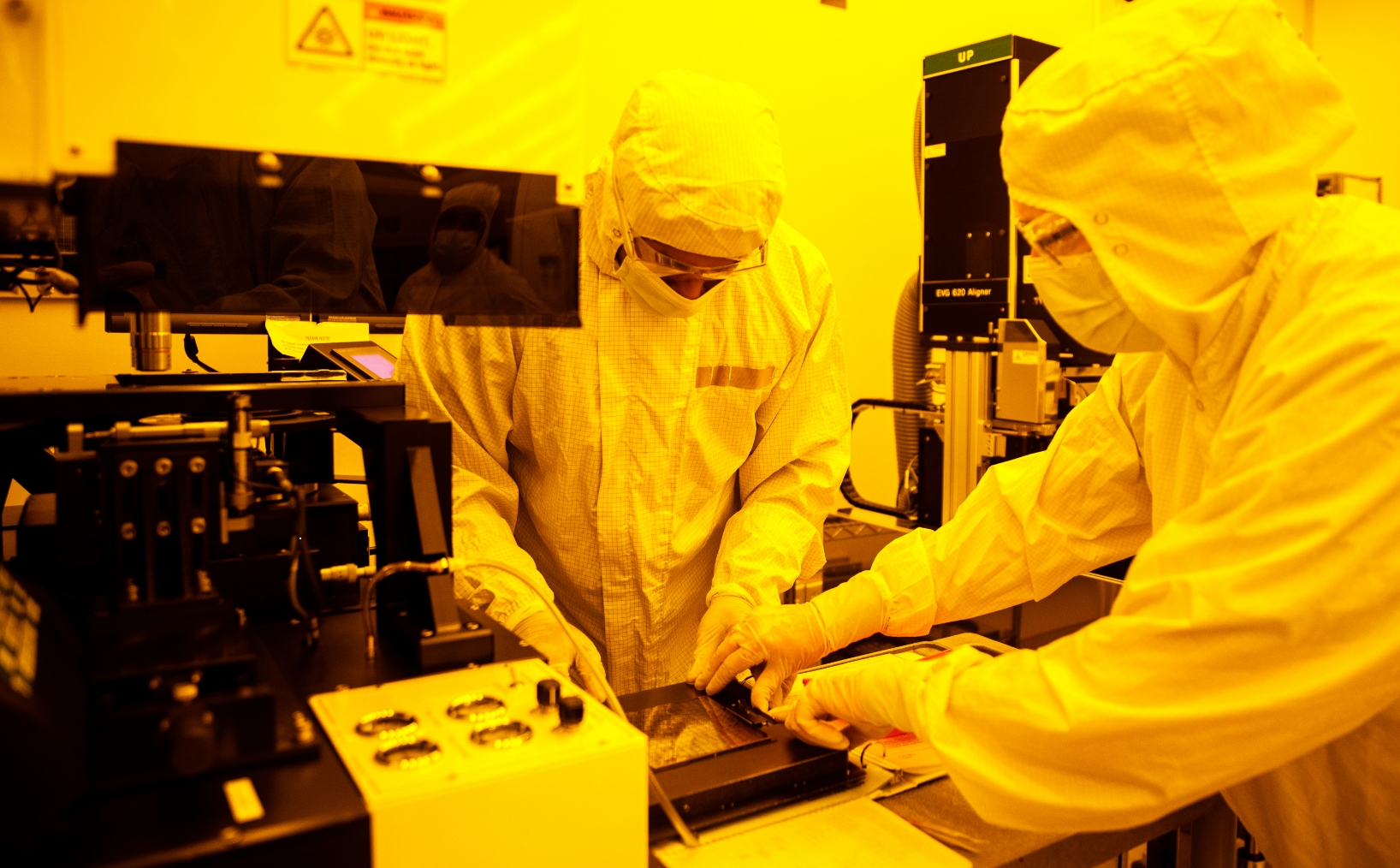
Core Research Facilities provide:
- One-stop access.
- Project development.
- Training and workforce development.
- Assistance with proposals and grant writing.
- Drop-off sample processing.
- Ad-hoc work.
Customized solutions
There is no one answer to every problem. We work with clients to address their specific needs with individualized solutions.
Ability to scale
We can assist in taking ideas from concept to completion, regardless of size or scope.
Consultation
Our team of experts can work with researchers to identify needs and develop custom scopes of work.
Stay in the know
Sign up for our newsletter to learn more about new equipment, services and events
that can advance your work.